Why Do You Need Rotary Drum Dryer When Making Fertilizer?
Rotary drum dryer is used for drying fertilizer pellets. It is suitable for various scales of fertilizer producing companies. You can use different heat sources according to the requirements of drying products, such as coal, natural gas, and biomass particles. This machine is suitable for all kinds of organic fertilizers and limestone with a moisture content of less than 80%.
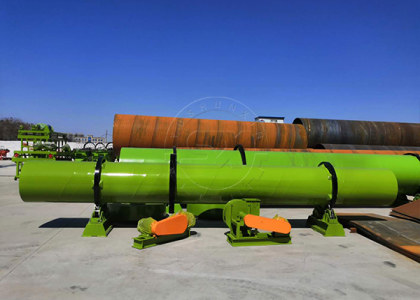
How Does A Rotary Drying Machine Work?
there is a rotating drum that is slightly inclined horizontally. the material is fed from the higher end. with the rotation of the cylinder, the material moves to the discharging end under the action of gravity. when the wet material moves forward in the cylinder, the rotary dryer receives heat from the heat sources directly or indirectly. in this way, the material is dried during this process and then sent out at the discharge end through a belt conveyor. there are many lift plates are designed inside the wall of the cylinder to increase the contact surface between the wet material and the airflow as well as improve the drying rate. meanwhile, these plates can scatter materials down.
Structures Of Rotary Drum Dryer
The rotary drum dryer is mainly composed of a heat source, an induced draft fan, a rotary drum, a braking device, a belt feeder, a feeder, a belt discharger, an unloader, and a power distribution cabinet. The structure is compact and easy to operate and maintain. It is made of carbon steel and specialty alloys, which makes it durable.
Main Parts of Rotary Drum Dryer
The rotary drum dryer is mainly composed of a heat source, an induced draft fan, a rotary drum, a braking device, a belt feeder, a feeder, a belt discharger, an unloader, and a power distribution cabinet. The structure is compact and easy to operate and maintain. It is of carbon steel and specialty alloys, which makes it durable.
Advantages Of Rotary Drum Dryer
The rotary drum dryer has a large processing capacity, efficient in fuel consumption and economical in cost. It has the characteristics of high-temperature resistance and can use hot air to dry materials in a short time. The adaptability is strong, and the design takes into account the production margin. Even if the output increases slightly, there is no need to replace the equipment. The specially designed wheel structure greatly reduces the horizontal thrust caused by the inclined operation of the equipment.
As the reducer of this dryer is provided by renowned manufacturers, the operation of the cylinder is not only stable but reliable.
WHAT IS THE HEAT SOURCE FOR ROTARY DRYER?
High temperature is necessary for the drying so the heat source is very important in the drying production line. Generally, many producers will choose coal, natural gas, biomass particles and electricity as the heat source of the rotary drum dryer.
Among these heat sources, the cost of coal is low, and natural gas and electricity are environmentally friendly. While as a new fuel, biomass particles are expensive. If you want to achieve energy-saving and environmentally friendly equipment operation, then natural gas is a very good choice.
Differnces Between 4 Heat Sources
- The air energy heat pump is a drying method that uses electricity as the heat source to absorb and convert air into heat. Air energy heat pump technology is becoming gradually popular due to its clean and pollution-free advantages.
- Natural gas is clean energy. In the case of full combustion, it mainly produces carbon dioxide and water and also produces a very small amount of sulfur dioxide and nitrogen oxides. Because the content is very low, the impact on the environment is very small and can be ignored. Therefore, the combustion exhaust gas of natural gas can be discharged directly without treatment, which is energy-saving and efficient. Therefore, as a heat source, natural gas has been more and more popular in the drying process.
- Biomass pellet fuel is a new energy fuel produced by processing straws, husks of crops and seeds, firewood, and corncob. It does not produce sulfur and phosphorus oxides during combustion, and will not cause acid rain. It produces less pollution to the environment. Furthermore, there is very little ash after fuel combustion, which can reduce the site for stacking slag. More importantly, after combustion, the ash of biomass pellet fuel is high-quality organic potassium fertilizer and you can recycle it for profit.
- Using coal as a heat source will generate a large amount of flue gas, and at the same time emit harmful gases, which will cause harm to the environment.
Why Drying Process Is So Important?
1. Reduce The Moisture Content Of Granular Organic Fertilizer
As we all know, the moisture content of organic fertilizer is relatively high. Although the moisture content of the material has been reduced during the stage of fermentation, crushing, mixing, and transportation, it has only been reduced to a moisture content that is more suitable for making granules. According to the “Organic Fertilizer Standard”, the moisture content of organic fertilizer is less than 30%. However, the processed particles contain moisture between 20% and 40% according to the characteristics of the material. In order to meet the standard, it is indispensable to dry them. Therefore, the pellet organic fertilizer production line is inseparable from the dryer and cooler.
2. Increase The Strength Of Fertilizer Granules
Granules with too low strength are unfavorable for the transportation of commercial packaging boxes. In the process of transporting, low strength will cause damage to the granules. Therefore, in order to meet the needs of packing, you need to dry the granular organic fertilizer after treatment.
3. Prolong The Storage Period Of Particles
It takes time to store from the beginning of packaging to the application of crops. It is necessary to ensure you can store the organic fertilizer as long as possible without reducing the nutrients of the fertilizer. The loss of nutrients is often caused by a reduction of particle strength, so the storage and transportation period of particles can be effectively extended after drying. Therefore, the drying process of the granular organic fertilizer production line is also good for prolonging the storage period of the particles.